Digital Assets and Operational Digital Twins
Andy Osborne
Digital Assets and Operational Digital Twins: Enhancing Efficiency in Industrial Operations
London, September 9th, 2023. In the era of digital transformation, industries are leveraging advanced technologies to optimize operations, enhance efficiency, and ensure compliance. Two essential concepts that play a pivotal role in achieving these goals are digital assets and operational digital twins. While they share some common ground, these concepts serve distinct purposes in industrial settings, contributing to the seamless functioning of operational facilities.
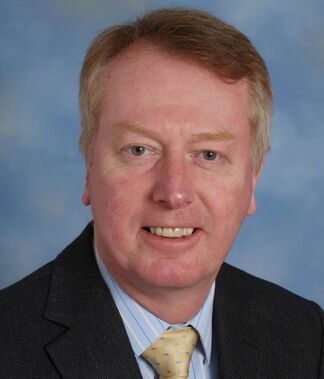
Andy Osborne, Senior Industry Consultant, is based in the UK. Andy began his career in engineering working for a Chemical owner operator and exploited new technologies that were available at the time to support project execution. He now has extensive experience in Global Business Development, Sales and Marketing with a focus on Engineering Applications and has worked for companies such as Alias Ltd, Intergraph, and Bentley Systems.
Digital Assets: The Blueprint of Operations
Imagine having a detailed blueprint that captures every facet of your industrial facility - from equipment layouts and specifications to process schematics and design data. This is precisely what digital assets offer. A digital asset is a digital representation of a physical object, system, or process. These assets comprise CAD drawings, 3D models, documentation, specifications, and more. They act as a comprehensive archive of your facility's configuration and serve as the backbone for various crucial aspects:
- Configuration Management: Digital assets provide a snapshot of your facility's layout and equipment. This documentation is invaluable for efficient maintenance, troubleshooting, and future expansions.
- Regulatory Compliance: In industries subject to stringent regulations, maintaining compliance is non-negotiable. Digital assets serve as evidence of adherence to regulations, simplifying audits and inspections by showcasing the correct installation of equipment and safety measures.
- Change Management: Operational facilities evolve over time due to upgrades, maintenance, or expansions. Accurate digital records streamline change management by ensuring modifications are well-planned and executed, reducing risks.
- Training and Collaboration: Onboarding new personnel becomes smoother with digital assets, allowing them to familiarize themselves with the facility's layout and processes before stepping foot on-site. Moreover, different teams can collaborate effectively using a centralized repository of information.
Operational Digital Twins: Real-Time Insight into Performance
Contrastingly, operational digital twins are real-time digital replicas of physical assets, systems, or processes. These twins integrate data from sensors, IoT devices, and other sources to mimic the behaviour of their physical counterparts. The benefits of operational digital twins are far-reaching:
- Real-Time Monitoring: Operational digital twins provide continuous insights into asset performance. They offer real-time data on equipment conditions, enabling proactive maintenance and reducing downtime.
- Analysis and Optimization: These twins facilitate in-depth analysis of asset behaviour. By simulating various scenarios, operators can optimize processes, leading to improved efficiency and resource utilization.
- Predictive Capabilities: Armed with historical and real-time data, operational digital twins enable predictive maintenance. This anticipates equipment failures, minimizing disruptions and maximizing uptime.
- Decision-Making: Informed decisions are critical in industrial operations. Operational digital twins provide a data-driven foundation for decision-making, enabling operators to respond swiftly to changing conditions.
In essence, digital assets act as the blueprint and documentation of an operational facility's configuration, and operational digital twins offer real-time insights and predictive capabilities. Together, they create a powerful synergy that drives efficiency, reliability, and compliance in industrial operations.
Embracing these concepts not only enhances day-to-day operations but also sets the stage for future innovations. By leveraging digital assets and operational digital twins, industries can unlock new levels of productivity, agility, and competitiveness in today's fast-paced business landscape.
The big issue is how you get to a point of having usable digital assets that can be leveraged in this way. Any inconsistencies between drawings and data, indexing of that data or any missing information will directly impact on the usability and adoption and acceptance of the daily use of such technologies.
Every company has a different start point and even facilities owned by that company will be unique in terms of what data is available, the specific formats of the data and how accurately it represents the physical asset. As previously discussed, there is no single automation technology that can accurately solve this issue without manual effort and expertise delivered through a service company such as TecSurge who have a focus on digital assets.
Moreover, TecSurge is in a unique position to support any company that wants to build a complete, consistent, and accurate Digital Asset, irrespective of your start point and end goal. Our 6 C’s Methodology is the template which is used to determine which specific activities need to be applied to address your individual circumstances, irrespective of how your current information is stored or your chosen platform. Our vendor independence as well as broad expertise and deep knowledge of engineering systems and information have stood us in good stead with a track record of delivering successful projects for more than 20 years.
Let’s talk!
If you are interested discussing what we can achieve working together, please leave a comment below or contact us.