Piping round-tripping: Importing piping fabrication data
by Patrick Mackinlay
Singapore, October 7th, 2020. In this fourth and final article of the series, I will describe a more modern approach to the import of piping fabrication data into the design environment.
In my previous article, I explained how isometric data files (IDFs) have been replaced by piping component files (PCFs), and how this technical detail did not change the conceptual information flow from design to fabrication. The same is true for the new implementation of the second part of the process, where the technical details have changed, but the concepts have fundamentally remained the same.
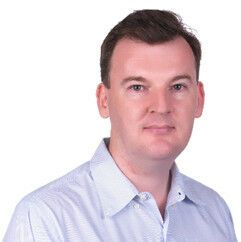
Patrick Mackinlay, Principal Consultant at TecSurge, directs product management and technology for the company. He holds a bachelor’s degree in Computer Science from Curtin University, and has over 20 years of experience in the plant design industry.
Prior to joining TecSurge, Patrick held senior technical and consulting roles with NRX and Intergraph, after 9 years with several EPCs as a systems analyst and administrator.
The historical approach to the reverse data flow relied upon spool sheet data files being generated by Spoolgen, containing information linking individual piping components in the PDS model with their assigned spool numbers. These data files were then manually transmitted back to the design office, after which the information contained could be imported (using custom developed software) into PDS, capturing the spool numbers against the model items and enabling their use in other downstream environments.
While spool sheet files are still able to be generated by Spoolgen, enhanced capabilities of the product offer two distinct improvements over the previous approach:
- Firstly, the data linking piping components to spool numbers is output in a new fabrication interface XML (FIX) file, which is both a more robust machine-readable format, and also contains information about weld types and locations, extending the range of information that can be round-tripped.
- Secondly, as described in my previous article, the FIX file is automatically recorded in the Spoolgen web service database, alongside the other deliverables, meaning no manual handling is required to make the data available to the design office.
Given this, the central requirement to implement this integration is to develop some clever custom software, to perform the following steps in a batch process:
- Identify and import the FIX files which need to be processed from the Spoolgen web service.
- Match the content of each FIX file with the corresponding Smart 3D piping elements.
- Evaluate whether the piping geometry contained within the FIX file matches the geometry in the Smart 3D model (and report an error if the geometry differs).
- Add, modify and delete welds in Smart 3D to correspond to those assigned in Spoolgen, potentially splitting and joining straight lengths of pipe in the process.
- Import spool and weld numbers from the FIX file into the weld-adjusted Smart 3D piping model.
Of course, several other details such as rolling back any changes in case of failure, ensuring that the Smart 3D PBS and WBS are correctly maintained, that appropriate approval status values are applied before and after processing, and reporting progress and problems to the operator are also essential to ensuring the system is robust and reliable.
The end result of applying this program is what we’ve been looking for: a Smart 3D model which contains the spool and weld information that’s been produced during fabrication. The immediate applications during capital project execution are fairly clear, and include providing construction with a more accurate representation of what is expected, and enabling additional options for gathering data, analysing progress and visualization.
Some potential benefits later in the life of the facility may also present themselves through the fact that all welds are fully accounted-for in the 3D model, making it possible to uniquely identify and track them for inspection or future capital works.
TecSurge is very proud to have played a key role in implementing and supporting this end-to-end piping round-tripping process for one of our valued clients, and we believe this innovation is likely to be of interest to many other companies who see its potential application and benefits.
If you have found these articles to be of interest, or have similar requirements in your own organization, please leave me a comment below or contact us to discuss the possibilities.