Piping round-tripping: 25 years ago
by Patrick Mackinlay
Singapore, July 16th, 2020. In this article, the second of the series, I will describe how piping round-tripping was achieved 25 years ago using PDS, Spoolgen and DesignReview and reflect on the tangible benefits produced.
I started this series of blog posts last month to write about a process I was personally involved with on a project about 25 years ago, and about its modern incarnation on a project that is currently being executed by one of our valued clients.
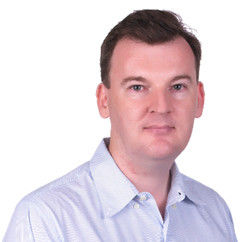
Patrick Mackinlay, Principal Consultant at TecSurge, directs product management and technology for the company. He holds a bachelor’s degree in Computer Science from Curtin University, and has over 20 years of experience in the plant design industry.
Prior to joining TecSurge, Patrick held senior technical and consulting roles with NRX and Intergraph, after 9 years with several EPCs as a systems analyst and administrator.
As many of you know, specification-driven 3D piping design and automated piping isometric drawing generation are not new ideas. For decades, the most common software used for the latter function has been Isogen, which is used in conjunction with a variety of plant design applications to produce piping isometrics, and also forms the heart of the Spoolgen companion product.
The fact that both applications are built on the same core technology enables efficient integrated workflows between piping design, fabrication, and construction organizations, such as the piping round-tripping process discussed here.
In this scenario, where the work process is implemented using PDS, the fundamental building block is the Isometric Data File (IDF) which is the primary input file for both Isogen and Spoolgen. In simple terms, PDS generates an IDF from the piping model representing the portion of piping to be issued and submits it to Isogen to generate an isometric drawing. This IDF is retained after the processing is complete, allowing it to be transmitted to a fabricator and reused as the input to Spoolgen.
At first glance, this may sound like a duplication of effort, but a closer inspection of the purpose of the deliverables produced at each stage of the process reveals important details. In most projects, the piping design office is not the most efficient environment to identify the best location for spool breaks, as the focus is on correct piping layout and design, and not on the ease of fabrication or installation of individual spools. The result is that the piping isometrics generated by the design office do not usually identify spool breaks, may not accurately represent weld types (e.g. field versus field-fit) and are used primarily to check the piping conforms to the P&ID and as a basis for controlling the release of piping for fabrication.
Conversely, the fabricator (typically in consultation with the constructor) will usually need to make decisions about where piping should be broken into spools, based upon ease of fabrication, handling, material availability and constructability. This function is one which is efficiently supported by the purpose-built Spoolgen application, especially because the fabricator can be certain that the as-designed piping is reproduced accurately and automatically from the IDF. Projects which do not use Spoolgen for piping fabrication must either use inefficient CAD or paper-based mark-up of the isometrics issued by the design office, or manually recreate the piping design and risk introducing errors.
The second part of the round-tripping process relies on this data flow, and on some of the technical information contained within the IDF as used by PDS, Isogen and Spoolgen. In particular, the fact that PDS uniquely identifies piping components with a Data Management and Retrieval System (DMRS) identifier and inserts these unique identifiers into the IDF makes round-tripping possible. When configured appropriately, Spoolgen can report the DMRS identifier of each component and the corresponding spool number assigned to an output file during processing. When these files are returned to the design office, and with the help of some custom developed software, the spool data can be imported back into the PDS model. This results in a data field in the piping model being populated with the spool number for each component (field materials are assigned to an otherwise unused spool number 0).
Now that I have explained how it can be accomplished even using these very old technologies, I want to discuss two key benefits that can be realised for projects to which this process is applied.
The first benefit is that having spool numbers in the piping model enables reporting from the design office, aligned with all the other useful attributes in the model (such as PBS, WBS, milestone/status, schedule, etc.). Having a properly controlled, validated and current source of spool numbers provides the required basis for tracking piping progress from fabrication, inspection, logistics, installation, testing and completion, in conjunction with other databases and applications designed to capture and report individual status data points. Trying to link these different information sources together without being able to rely on such an integrated and stable source of truth presents significant challenges.
The second benefit lies in extending the value of the visualization model common to projects executed in 3D by including spool number information. In the project I’ve referred to earlier, one example of this was delivered by using DesignReview functionality to apply a rainbow of different colours to piping components based upon their assigned spool numbers, so that it became instantly obvious where spool breaks were positioned. This effect added significant value to the visualization environment for construction contractors, allowing them to more quickly assess and plan scaffolding, rigging, lifting, and welding activities.
The combination of these two benefits provides the basis for a third, not realised in my project example, but which clearly has potential value: a visual interface for piping construction progress capture. With contemporary technology, it is easy to imagine how this can be taken even further, with an augmented-reality overlay of colour-coded piping spools against the physical construction enabling simple point-and-shoot selection of spools to query or update status information.
Describing what was able to be achieved using technology available 25 years go and the benefits of the piping round-tripping process has been the focus of this article. Next time, I will take a closer look at the first part of the piping round-tripping process in a more contemporary context.
Look out for these blogs:
- Piping round-tripping: Issuing piping design data
- Piping round-tripping: Importing piping fabrication data
If you are interested to discuss what we can achieve working together, please leave me a comment below or contact us.