Piping round-tripping: Issuing piping design data
by Patrick Mackinlay
Singapore, August 26th, 2020. In this article, the third of the series, I will describe how the first part of the piping round-tripping process has evolved, and how improved technologies can streamline the flow of data.
Previously, I glossed over some of the details involved in transferring the piping design data (in the form of Isometric Data Files) from the piping design office to the fabricator. In practice, because the interface between the producing and consuming software was file-based, the task of delivering this data fell to traditional document control methods:
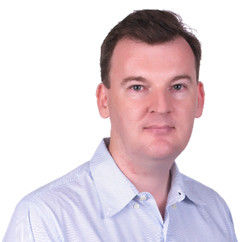
Patrick Mackinlay, Principal Consultant at TecSurge, directs product management and technology for the company. He holds a bachelor’s degree in Computer Science from Curtin University, and has over 20 years of experience in the plant design industry.
Prior to joining TecSurge, Patrick held senior technical and consulting roles with NRX and Intergraph, after 9 years with several EPCs as a systems analyst and administrator.
- Piping department generate, extract and bundle (e.g. ZIP) IDFs for transmission
- Document control at the design office prepares a transmittal and associates the bundle
- Transmittal and data is delivered via some kind of file transfer service (e.g. FTP, email)
- Document control at the fabrication office unbundles, checks and distributes the data
- Fabrication drawing office imports IDFs into Spoolgen for processing
While this is a familiar and stable process, it’s clear it involves significant human effort and is ripe for improvement by the application of more modern tools.
One of our valued clients has recently seized this opportunity, and with the assistance of TecSurge, constructed a more seamless and efficient end-to-end data flow built upon two key technologies. Since the project is being executed in 2020 rather than 1995, the source of the piping data is Intergraph Smart 3D rather than PDS, and the information is contained in Piping Component Files (PCF) rather than the conceptually equivalent IDF, but conceptually the round-tripping process is unchanged.
The first element of the improved process relies upon the integration of Smart 3D with SmartPlant Foundation (SPF), which enables the automated transfer of PCFs and piping meta-data to be driven by a “publish” action from the piping department.
The second step in the improved process is built upon the database which has been added to the Spoolgen application, and its associated web service. This database holds all of the data and meta-data traditionally managed by Spoolgen, and supports a check-in/check-out paradigm to ensure this centralized information source is properly controlled. The web service provides automated, distributed access to this information in a secure fashion to all authorized parties.
Together, these tools are combined to produce a much more seamless data flow:
- Piping department “publishes” piping from Smart 3D to SmartPlant Foundation, and from there use a custom-built web client function to select and transmit PCFs to fabricators (based on work package association)
- Automation imports the transmitted PCFs directly from SPF into the Spoolgen central database under a project assigned to the relevant fabricator
- Fabricators use the “check-out” feature of Spoolgen to download PCF data from the central database to their local workstation across the internet to generate the fabrication deliverables needed, checking in their completed work
Of course traditional-looking records are captured along the way to document the process, however these automated data transfers accelerate and remove much of the manual effort and potential for error of the process described earlier.
An additional benefit of this process is that the results of the fabricator’s task are also transparent to project management, and a variety of different deliverables or reports can be extracted at any time to gain insight into project progress or other metrics.
While these new tools offer powerful raw functionality, the configuration, customization, testing and support needed to implement such advanced, integrated, and project-specific data flows successfully requires an in-depth understanding of both the technologies and work processes. TecSurge is proud to have played a key role in implementing this process for one of our clients, and we are keen to bring our expertise to assist others who have similar requirements.
Describing what is possible using contemporary technology to improve the issue of piping design data within the overall piping round-tripping process has been the focus of this article. Next time, I will describe a contemporary take on the second part of the process, in importing piping fabrication information into the design environment.
You are reading the third in a series of four blog posts. Look out for the fourth blog coming soon:
- Piping round-tripping: Introduction
- Piping round-tripping: 25 years ago
- Piping round-tripping: Issuing piping design data
- Piping round-tripping: Importing piping fabrication data
If you are interested to discuss what we can achieve working together, please leave me a comment below or contact us.