Industry 4.0: Our perspective
by Patrick Mackinlay
Singapore, February 20th, 2019. We recognise that digital transformation and industry 4.0 have gained a huge amount of attention around the world in recent years. That is why I want to take this opportunity to explain how we understand these trends and their place in our industry, what challenges our clients face, and how we can help.
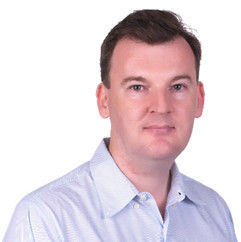
Patrick Mackinlay, Principal Consultant at TecSurge, directs product management and technology for the company. He holds a bachelor’s degree in Computer Science from Curtin University, and has over 20 years of experience in the plant design industry.
Prior to joining TecSurge, Patrick held senior technical and consulting roles with NRX and Intergraph, after 9 years with several EPCs as a systems analyst and administrator.
In this blog, I will focus on giving our perspective on what industry 4.0 involves, and how it intersects with the process industry.
Industry 4.0 was originally a high-tech strategy defined by the German government to computerize manufacturing. From that starting point, it has grown to have a significant influence and impact upon industrial companies of all kinds. It is based on four key principles:
- Firstly, the ability of machines, devices, sensors and people, to connect and communicate with each other, often referred to as the Internet of Things, or IoT.
- Next is the transparency of information derived by collecting massive amounts of real-time operational data enabled by this interconnectivity.
- Thirdly, is the decentralization of decision making, enabling devices and systems to operate autonomously, and only involving humans when exceptions or conflicting priorities arise.
- Finally, the aggregation and visualization of collected data enables people to make informed decisions and solve urgent problems, and to automate dangerous or unpleasant tasks.
Unlike manufacturing, process industries have taken advantage of three of these principles for decades. The use of process instrumentation, computerised historian and operations systems, and distributed control systems are all standard features of today’s process plants.
We believe that significant business value in the process sector can be unlocked by exploiting opportunities for technical assistance, through the aggregation and visualisation of engineering data. Examples range from the use of machine learning technologies to optimize plant design and operational performance, through virtual and augmented reality systems for remote operation and training, to the use of autonomous vehicles on plant sites.
All these opportunities rely upon a foundation of accurate, complete and available digital information representing the physical plant. This representation is commonly described as a digital twin, or a living digital twin when combined with real-time operational data.
The challenge faced by most operators is that existing engineering data is inaccurate, incomplete, or locked in proprietary or legacy systems. Solving this problem is a key prerequisite to moving ahead with digital transformation plans.
If you would like to discuss this topic further, please leave me a comment below or contact us via our web site or email.